Co to jest anodowanie aluminium?
Anodowanie aluminium to proces elektrochemiczny. Polega on na kontrolowanym tworzeniu warstwy tlenku na powierzchni aluminium. Proces ten zachodzi poprzez poddanie aluminium działaniu prądu elektrycznego w specjalnie przygotowanej kąpieli elektrolitycznej. Składa się on z dwóch głównych etapów. W pierwszym etapie aluminium działa jako anoda. W drugim etapie katoda może być wykonana z innego materiału przewodzącego prąd. Na przykład może to być aluminium, stal lub tytan.
W trakcie anodowania aluminium ulega reakcji elektrochemicznej. W efekcie na jego powierzchni tworzy się warstwa tlenku. Warstwa ta jest bardzo cienka i mikroporowata. Dzięki temu pozwala na różne możliwości wykorzystania. Proces anodowania jest kontrolowany pod względem różnych parametrów. Należą do nich czas trwania, temperatura, skład elektrolitu oraz prąd elektryczny. Dzięki tej kontroli możliwe jest uzyskanie warstwy o dokładnie określonej grubości i strukturze.
W zależności od parametrów procesu można osiągnąć różne właściwości warstwy anodowej. Mogą to być na przykład twardość, odporność chemiczna oraz estetyka. Anodowanie aluminium jest szeroko stosowaną techniką. Ma zastosowanie zarówno w przemyśle, jak i w produkcji elementów konsumenckich. Wynika to z jego zdolności do poprawy zarówno ochrony, jak i wyglądu aluminium.
Zalety anodowania aluminium
Odporność na korozję
Anodowane aluminium charakteryzuje się wyjątkową odpornością na korozję. Warstwa tlenku tworząca się podczas procesu anodowania stanowi skuteczną barierę, chroniącą aluminium przed działaniem wilgoci, substancji chemicznych i korozją atmosferyczną. Dzięki temu produkty wykonane z anodowanego aluminium zachowują swoją integralność i estetyczny wygląd nawet w trudnych warunkach środowiskowych.
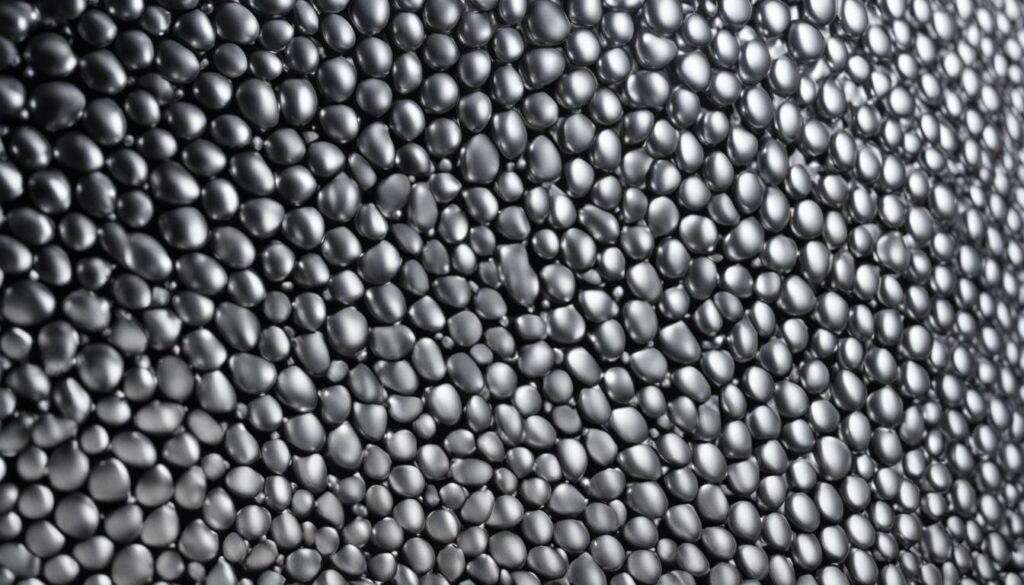
Twardość i trwałość
Warstwa tlenku tworzona podczas anodowania znacznie zwiększa twardość aluminium. Jest to szczególnie istotne w przypadku produktów narażonych na działanie mechaniczne, np. elementów konstrukcyjnych czy narzędzi. Anodowane aluminium jest bardziej odporne na zarysowania, ścieranie i uszkodzenia, co przekłada się na wydłużenie trwałości i użytkowej żywotności produktów.
Niska waga
Pomimo zwiększenia twardości, anodowane aluminium nadal pozostaje lekkie. Ta kombinacja wytrzymałości i niskiej wagi sprawia, że jest ono atrakcyjnym materiałem konstrukcyjnym w wielu dziedzinach przemysłu, takich jak transport, lotnictwo czy produkcja urządzeń sportowych. Dzięki niskiej wadze, anodowane aluminium umożliwia projektowanie produktów o niższym zużyciu energii oraz mniejszym wpływie na środowisko.

Estetyka i personalizacja
Anodowanie aluminium oferuje szeroki wachlarz możliwości estetycznych. Proces ten umożliwia barwienie aluminium na różne kolory oraz uzyskanie różnorodnych wykończeń, takich jak matowe, błyszczące czy metaliczne. Dzięki temu producenci mogą dostosować wygląd swoich produktów do indywidualnych preferencji estetycznych klientów, co sprawia, że anodowane aluminium znajduje zastosowanie w wielu branżach, od motoryzacji po elektronikę użytkową.
Estetyka anodowanego aluminium
Wykończenia
Anodowane aluminium może mieć różnorodne wykończenia, od matowych po błyszczące i metaliczne. Dzięki temu producenci mają możliwość dostosowania wyglądu swoich produktów do konkretnych potrzeb i oczekiwań klientów. Matowe wykończenia nadają produktom elegancki, nowoczesny wygląd, podczas gdy wykończenia błyszczące mogą dodawać im prestiżu i luksusowego charakteru.

Różnorodność kolorów
Anodowanie aluminium umożliwia uzyskanie szerokiej gamy kolorów, co otwiera przed projektantami i producentami niemal nieograniczone możliwości w kwestii personalizacji i dopasowania produktów do określonych stylów i preferencji estetycznych. Proces ten pozwala na uzyskanie intensywnych, trwałych kolorów, które nie blakną pod wpływem warunków atmosferycznych, co jest szczególnie istotne w przypadku zastosowań zewnętrznych.
Trwałe efekty
Warstwa tlenku utworzona podczas anodowania aluminium nie tylko chroni przed korozją, ale również zapewnia trwałe efekty estetyczne. Kolory i wykończenia anodowanego aluminium są odporne na blaknięcie, ścieranie i działanie warunków atmosferycznych, co sprawia, że produkty zachowują swój atrakcyjny wygląd przez długi czas bez konieczności częstej konserwacji czy wymiany.

Możliwości personalizacji
Anodowane aluminium umożliwia także dodanie indywidualnych wzorów, logo lub tekstów na powierzchni produktów poprzez techniki druku lub grawerowania. To pozwala na jeszcze większą personalizację i zwiększenie atrakcyjności wizualnej produktów dla klientów, co może być kluczowe w przypadku produktów dedykowanych marketingowi lub prezentacji marki.
Anodowanie aluminium w praktyce
Budownictwo
W branży budowlanej anodowane aluminium stosuje się do produkcji okuć okiennych i drzwiowych, balustrad, elementów elewacyjnych oraz innych detali architektonicznych. Dzięki swojej trwałości, odporności na warunki atmosferyczne i estetycznemu wykończeniu, anodowane aluminium sprawdza się zarówno w zastosowaniach zewnętrznych, jak i wewnętrznych, nadając budynkom nowoczesny i elegancki wygląd.

Przemysł motoryzacyjny
Anodowane aluminium znajduje szerokie zastosowanie w przemyśle motoryzacyjnym. Odgrywa rolę w produkcji elementów wykończeniowych, jak listwy ozdobne, felgi czy elementy wnętrza pojazdów. Dzięki swojej odporności na korozję i możliwości personalizacji kolorystycznej. Anodowane aluminium spełnia wymagania estetyczne i funkcjonalne, zarówno w przypadku luksusowych limuzyn, jak i samochodów sportowych.
Elektronika i urządzenia konsumenckie
W elektronice i produkcji urządzeń konsumenckich anodowane aluminium wykorzystuje się do obudów telefonów komórkowych, laptopów, tabletów, a także do akcesoriów takich jak obudowy odtwarzaczy muzycznych czy klawiatury komputerowe. Dzięki swojej lekkości, trwałości i estetycznemu wykończeniu, anodowane aluminium spełnia wymagania klientów związane zarówno z funkcjonalnością, jak i designem.
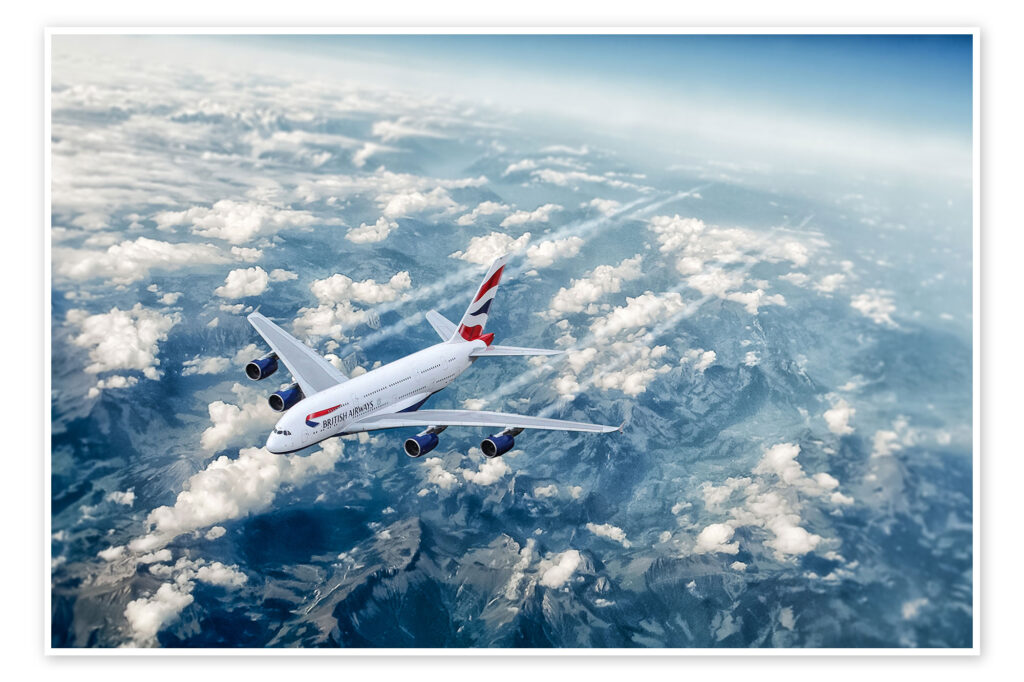
Przemysł lotniczy i kosmiczny
Anodowane aluminium znajduje zastosowanie również w przemyśle lotniczym i kosmicznym, gdzie jest używane do produkcji części konstrukcyjnych, obudów elektronicznych oraz elementów wykończeniowych w samolotach, rakietach i satelitach. Jego niska masa i wysoka wytrzymałość sprawiają, że jest idealnym materiałem do zastosowań, gdzie każdy gram ma znaczenie, a jednocześnie zapewniającym niezawodność i estetykę.
Podsumowanie
Podsumowując, anodowanie aluminium to nie tylko skuteczna metoda ochrony przed korozją, ale również środek do poprawy estetyki produktów. Proces ten oferuje szereg zalet, takich jak odporność na korozję, twardość, trwałość oraz możliwość personalizacji kolorystycznej i wykończeniowej. Zastosowanie anodowanego aluminium jest wszechstronne i obejmuje wiele branż, od motoryzacji przez budownictwo po elektronikę i przemysł lotniczy. Dzięki swoim właściwościom anodowane aluminium stanowi niezawodne rozwiązanie. Pod względem funkcjonalnym, jak i estetycznym, spełniając najwyższe wymagania klientów i producentów.
Często Zadawane Pytania o Anodowanie Aluminium
Co to jest anodowanie aluminium? Anodowanie aluminium to proces elektrochemiczny, w którym aluminium jest poddawane działaniu prądu elektrycznego w celu tworzenia warstwy tlenku na jego powierzchni. Ta warstwa tlenku ma właściwości ochronne i estetyczne.
Jakie są główne korzyści anodowania aluminium? Główne korzyści anodowania aluminium obejmują jego wysoką odporność na korozję, twardość, trwałość oraz możliwość personalizacji kolorów i wykończeń.
Czy anodowane aluminium jest odporne na korozję? Tak, anodowane aluminium jest znacznie bardziej odporne na korozję niż aluminium nieanodowane. Warstwa tlenku tworzona podczas anodowania działa jako skuteczna bariera chroniąca przed wilgocią i innymi czynnikami atmosferycznymi.
Jakie są dostępne wykończenia anodowanego aluminium? Anodowane aluminium może mieć różne wykończenia, w tym matowe, błyszczące i metaliczne. Istnieje również szeroka gama kolorów do wyboru, co umożliwia dopasowanie do indywidualnych preferencji estetycznych.
Gdzie stosuje się anodowane aluminium? Anodowane aluminium znajduje zastosowanie w wielu branżach, w tym w przemyśle motoryzacyjnym, budownictwie, elektronice, przemyśle lotniczym i kosmicznym, a także w produkcji artykułów konsumenckich.
Czy anodowanie aluminium wpływa na jego właściwości mechaniczne? Tak, anodowanie aluminium może zmienić niektóre właściwości mechaniczne aluminium, takie jak twardość i wytrzymałość na ścieranie. Jednakże, w większości przypadków, te zmiany są korzystne i poprawiające jakość.
Czy anodowanie aluminium jest trwałe? Tak, warstwa tlenku utworzona podczas anodowania aluminium jest trwała i odporna na blaknięcie, ścieranie oraz działanie warunków atmosferycznych. Dzięki temu, anodowane aluminium zachowuje swój estetyczny wygląd przez długi czas.
Czy anodowanie aluminium wpływa na jego wadze? Anodowanie aluminium nie znacząco wpływa na jego wagę. Pomimo zwiększenia twardości, anodowane aluminium nadal pozostaje lekkie, co sprawia, że jest atrakcyjnym materiałem w wielu zastosowaniach, gdzie masa ma znaczenie.